General Purpose
Variable Frequency Drives
High Performance
Variable Frequency Drives
Application Specific
Variable Frequency Drives
Designed to be cost effective and easy to use, the Optidrive E3 Single Phase is for use with PSC (permanent split capacitor) or shaded-pole single phase induction motors.
OptiTools Studio is a powerful commissioning and programming application, compatible with most current Optidrive products.
Peripherals, installation and network options designed to complement the Optidrive range.
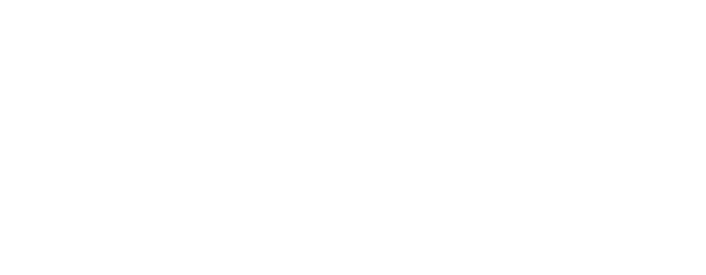
What is a Variable Frequency Drive?
Article
1
1
Explore 'how to' videos and tutorials; search an extensive database of installation, commissioning and application advice; and check for our engineers' responses to FAQs about variable frequency drives.