Textiles & Paper applications
Our VFDs are used in textiles and paper manufacturing all over the world to deliver precise process control and energy savings.
Control of motor speed
VFDs allow precise control of motor speed by adjusting the frequency and voltage. This feature is beneficial in textile and paper manufacturing processes that require different speeds for various operations such as winding, weaving, cutting, and coating. By controlling motor speed, VFDs enable manufacturers to achieve better product quality, reduce defects, and enhance process efficiency.
Energy savings
VFDs are highly efficient in controlling motor speed, reducing the energy consumption of electric motors. In textile and paper manufacturing, where motors are used extensively, implementing VFDs can result in significant energy savings. By matching motor speed with the required load, VFDs eliminate the need for throttling devices or mechanical control mechanisms, leading to reduced energy wastage.
Process optimisation
VFDs provide flexibility in adjusting motor speed and torque to optimise various manufacturing processes. In textile production, VFDs can regulate the speed of spinning machines, looms, and dyeing equipment to ensure precise yarn tension, reduce material waste, and improve the consistency of the final product. In paper manufacturing, VFDs enable control of motor speed in pulp and paper processing stages, facilitating smoother operations and better product quality.
Soft start and stop
VFDs allow gradual acceleration and deceleration of electric motors, resulting in soft starts and stops. This feature minimizes mechanical stress, reduces wear and tear, and extends the lifespan of motors and associated equipment. In textile and paper manufacturing, where delicate fibres and paper sheets are involved, soft starts and stops provided by VFDs prevent damage and increase the overall equipment reliability.
Synchronisation and coordination
VFDs enable synchronised operation of multiple motors in textile and paper manufacturing processes. By controlling the frequency and speed of individual motors, VFDs ensure coordinated movement and synchronisation of various components and machines. This synchronisation is critical in processes such as printing, coating, and laminating, where precise alignment and timing are essential for achieving uniform and high-quality results.
Diagnostic and monitoring capabilities
Advanced VFDs often come with built-in diagnostic and monitoring features. They can collect and analyse motor performance data, detect abnormalities, and provide real-time feedback on motor health and energy consumption. By utilising these capabilities, textile and paper manufacturers can proactively identify potential issues, conduct preventive maintenance, and optimise energy usage, leading to improved overall equipment effectiveness (OEE) and reduced downtime.
Sumitomo Drive Technologies - products for Textiles & Paper
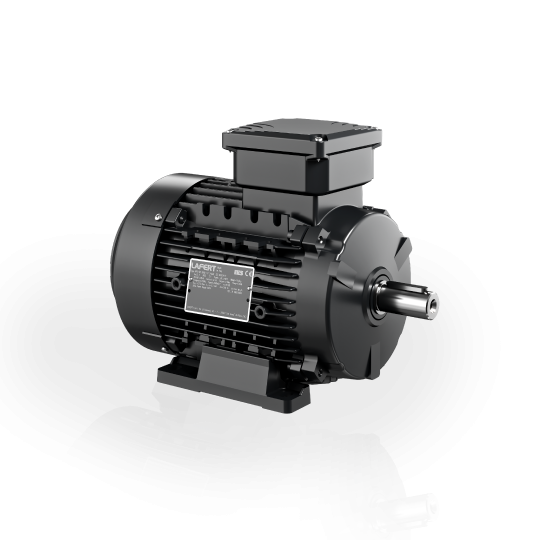