Refrigeration Compressor Control
We have vast experience delivering the right variable frequency drives into refrigeration compressor control applications.
Refrigeration Compressor control without compromise
High efficiency, high performance cooling capacity control
Using a variable frequency drive for precise, energy efficient control of refrigeration compressors can dramatically reduce energy consumption and improve system COP (Coefficient of Performance).
If a compressor fails it can often have catastrophic consequences for the rest of the production process. Using a variable frequency drive to vary the compressor speed to match demand also increases system reliability.
- Improve system performance
- Reduce energy costs
- 20% free cooling capacity
- Extended compressor life
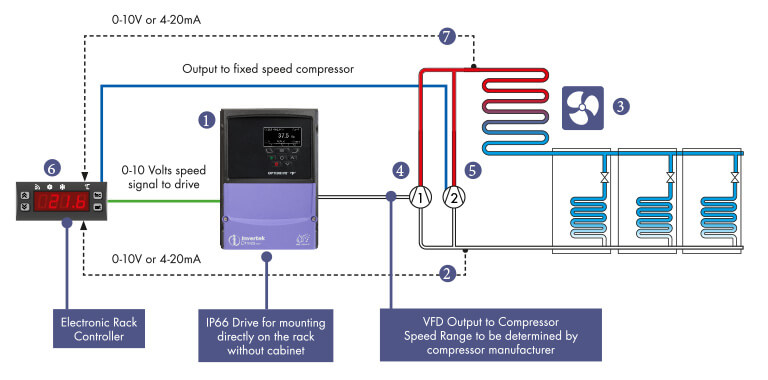
Compressors are used in a wide range of HVAC-R systems, providing cooling and heating (reversable heat pumps) for industrial, commercial & food retail applications. In the past, cooling was delivered by running the fixed speed compressor to meet the cooling demand of the system, and then turning it off when the desired cooling had been reached. This type of system control, uses a thermostat to turn the compressor on and off. A good example of this type of control is the domestic fridge. This method of “on-off” capacity control is still used today, but is very inefficient.
Match cooling capacity to changing system demand
The introduction of AC variable frequency drive technology, allows HVAC-R machine builders and system integrators to vary the cooling capacity of the compressor by changing the compressor speed, to accurately maintain the cooling requirement. This is achieved by fitting a pressure transducer into the low pressure suction line. The transducer measures the suction pressure and the controller compares the actual pressure to the required set-point. The controller subsequently adjusts the compressor’s speed to run faster or slower, by varying the 0 to 10V or 4…20mA speed demand signal to the OPTIDRIVE™, to maintain the system set-point during periods of high and low cooling demand.
4% energy saved for every 1-degree kelvin improvement
This method of smooth capacity control provides improved system stability, by reducing the under and overshoot around the set-point, which is common with “on-off” control systems. It has been calculated, that by reducing the error around the set-point, by using OPTIDRIVE™, for every 1-degree Kelvin improvement, the user can save 4% in energy consumption. In supermarket applications, providing a stable temperature inside their refrigerated display cases, extends product life, and lowers costs associated with food wastage.
20% free additional cooling capacity
20% free additional cooling capacity can be achieved on an existing fixed speed compressor connected to a 50Hz supply, by simply installing an OPTIDRIVE™ variable frequency drive. Most compressor motors are designed for 50Hz or 60Hz supplies. The OPTIDRIVE™ allows the maximum output speed of the compressor to be safely increased from 50Hz to 60Hz. Compressor capacity increases proportionally to output speed. Therefore, setting the OPTIDRIVE™ output frequency to 60Hz, the cooling capacity is increased by 20%. If the compressor being controlled by the variable frequency drive is on the lead compressor, on a multi-compressor refrigeration rack system, it is possible to increase the output speed of the compressor beyond 60Hz. Semi hermetic compressors, can run safely at output speeds of 65Hz to 70Hz, providing 30% - 40% free cooling capacity. The maximum & minimum output speed should always be confirmed by contacting the compressor manufacturer.
Extended compressor life
Increasing the output speed, and thereby the cooling capacity, could result in the second fixed speed compressor on the rack, operating less often. This results in lower energy costs, improved system control, and extended compressor life, due to fewer starting cycles. OPTIDRIVE™, ideal for OEMs and also refrigeration contractors & installers for retrofit applications, providing a cost effective and energy efficient solution to control the cooling capacity of the compressor to correspond with the varying system demand. It can be supplied enclosed as IP20 for OEMs to install in their electrical control panel, or IP66, which allows the OEM or contractor and installer to mount OPTIDRIVE™ on the wall, inside the electrical switch room, or directly on the compressor rack. This eliminates the need for an electrical control panel, lowering cost.
Food and Beverage
We have vast experience delivering the right variable frequency drives into food and beverage applications.
In the food and beverage sector refrigeration is often the biggest single energy consuming element. Food safety, maximum energy efficiency and control of systems using natural refrigerant solutions are all priorities of any refrigeration control system, with variable frequency drives needing to provide precise monitoring and management solutions to meet these requirements.
- Improve energy efficiency
- Ensure food safety
- Monitoring and alert
-
Display cases and cold rooms
Efficient refrigeration systems optimised for CO2 and other natural refrigerants require precise control that minimise cost of ownership whilst reducing the carbon footprint of refrigeration systems.
Commercial and Industrial Cold Chain
We have vast experience delivering the right variable frequency drives into commercial and industrial cold chain applications.
Commercial and industrial refrigeration covers a wide range of applications that supply chains rely on. Food safety in the dairy, fisheries and meat processing sectors require a seamless and reliable cold chain – from the point where product is harvested to when it is delivered to the consumer. A precisely controlled, uninterrupted cold chain is also a necessity for the pharmaceutical industry.
In these markets, retailers, manufacturers, producers, logistics and transport operations and OEM’s all require a wide range of energy efficient and reliable refrigeration control solutions.
- Maintain the cold chain
- Protect perishable goods
- Operate in a wider variety of climates
- Effectively control systems with CO2 and natural refrigerants
Sumitomo Drive Technologies - products for Refrigeration
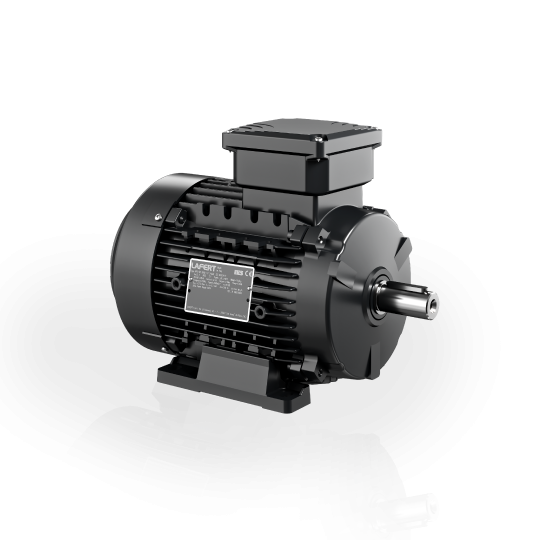