Motors, Motors, Motors
Article 12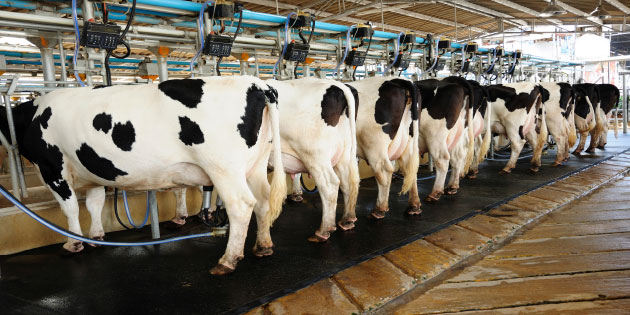
We discussed in an earlier article that variable frequency drives were designed to control induction (also known as asynchronous) motors. These are simple, cheap and reliable, and are the workhorse of industry worldwide. However, recent advances in technology have encouraged the development of many other types of motor which can be controlled by a drive. These motors often are more suited to particular applications, or are increasingly chosen because they are more efficient. But don’t forget that induction motors are also improving in efficiency. An efficient motor means less waste heat at the motor, possibly a smaller motor, but most importantly, a reduction in energy bills.
So what sort of new motors are we talking about?
Permanent Magnet Motors
Permanent magnet motors (PMMs) have been around for some time. Basically, the induction motor rotor – which consists of a simple cast winding embedded in steel laminations – is replaced by a series of permanent magnets, as shown in Figure 1.
.jpg)
Apply a variable frequency supply to the stator windings, and the rotating magnetic field will interact with the magnets in the rotor to produce torque. There’s no current in the rotor now, so there are no rotor losses, which makes the PMM more efficient, and possibly smaller.
However, controlling them is not as straightforward as controlling an induction motor. There is less inherent damping in a PMM, so there is a greater tendency for torque pulsation. To control this, the variable frequency drive really needs to be operated in Vector control. We’ll look at this detail in a later article, but suffice to say that controlling the torque and flux levels ‘on the fly’ – using vector control – results in nice smooth operation of PMMs.
It is also useful to detect the positions of the magnets in the rotor at start up to give a smooth start and good running. Software in the drive will do this, but leads to a slight delay in starting.
There’s been some concern about the price and availability of the rare earth elements that make up the rotor magnets in a PMM. Actually, it’s not that they are rare, but more that there are limited sources, largely in China. New sources are opening up, and other magnetic materials are under consideration, but PMMs will always be more expensive than traditional induction motors. However, their increased efficiency and (in some cases) smaller size means many users are adopting them in many applications. PMMs are now a standard offering from many motor manufacturers.
Synchronous Reluctance Motors
A Synchronous Reluctance Motor (SRM) goes one step further. The rotor now consists only of carefully shaped steel laminations, as shown in Figure 2.
.jpg)
The magnetic field from the stator windings magnetise corresponding sections of the rotor in the same way a simple horseshoe magnet magnetises a steel nail. Again, the interacting field produces Torque, which rotates the shaft. Like the PMM, an SRM needs careful control to reduce torque pulsation, so Vector control is preferred. And like the PMM, there are virtually no rotor losses, so motor efficiency is higher than an equivalent induction motor, and the higher cost of the motor can be justified by reduced energy usage and rapid payback times.
By the way don’t confuse Synchronous Reluctance Motors with Switched Reluctance Motors. A switched reluctance motor requires a slightly different power electronics configuration and also needs rotor position feedback. They tend to be noisy and suffer from torque pulsations; however, the motor can be very cheap and robust.
Brushless DC Motors
Brushless DC can refer to many different types of motor (including PMMs) where the commutator of a DC motor is replaced by electronic switching such as a drive. Brushless DC Motors (BLDCM) are essentially the same as PMMs, but the name often refers to motors constructed ‘inside out’. That is, the stator is on the inside of the motor, and is fixed. The rotor, containing the magnets, is on the outside.
.jpg)
This arrangement is particularly convenient for applications such as small cooling fans. Again, BLDCMs must be driven by some form of variable frequency drive. In a small fan application the drive system will be built into the stator assembly, and may well use a sensor to detect the position of the rotor. These types of BLDCMs are driven by simple square wave inverters controlled by feedback from the sensor. These motors are effectively fed with AC, so brushless DC is a bit of a misnomer. But as the sensor switches each stator winding on and off via the inverter as the rotor goes round, they are a bit like a DC motor with an electronic switch instead of a commutator and brushes. Hence their other name, Electronically Commutated DC motors. Larger BLDCMs with stators on the outside are driven in the same way as PMMs; they can operate without sensors providing the variable frequency drive can detect the rotor position and speed by using vector control. The drive may produce a waveform more like a square wave to optimise the motor performance.