Supplies and Supply Problems
Article 21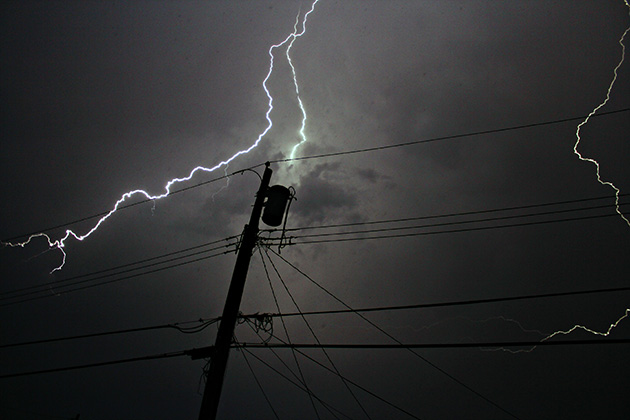
The variable frequency drive needs power. Not just a few Watts, but kilowatts to turn the motor, plus a bit to run itself. Nearly all drives get their power from ‘the mains’, but we’ll see there’s more to this than just connecting to the supply. And if there’s no mains available, there are other possibilities that can be used - with care.
Drives don’t generally step up or step down voltage, so whatever goes into them is generally about the voltage that comes out. There is an exception to this; some drives will accept a 110V input and double the voltage to produce a 230V output; but let’s stick to mainstream products for the moment.
So a 230V AC rated drive will produce about 230V three phase output (variable frequency and voltage of course) which is suitable for a 230V three phase motor. Many motors can be configured for 230V (delta connection) or 400V (star connection), so make sure your motor is correctly connected. Larger motors may be configurable for 400V and 690V, or simply one voltage, so check the rating label and the link settings before you connect up.
Back to the variable speed drive. Single phase and three phase input drives are available at 230V, so again make sure you have the right drive. Inside the drive the AC is converted immediately to DC by the rectifier diodes which sense the peak voltage, as shown in Figure 1.
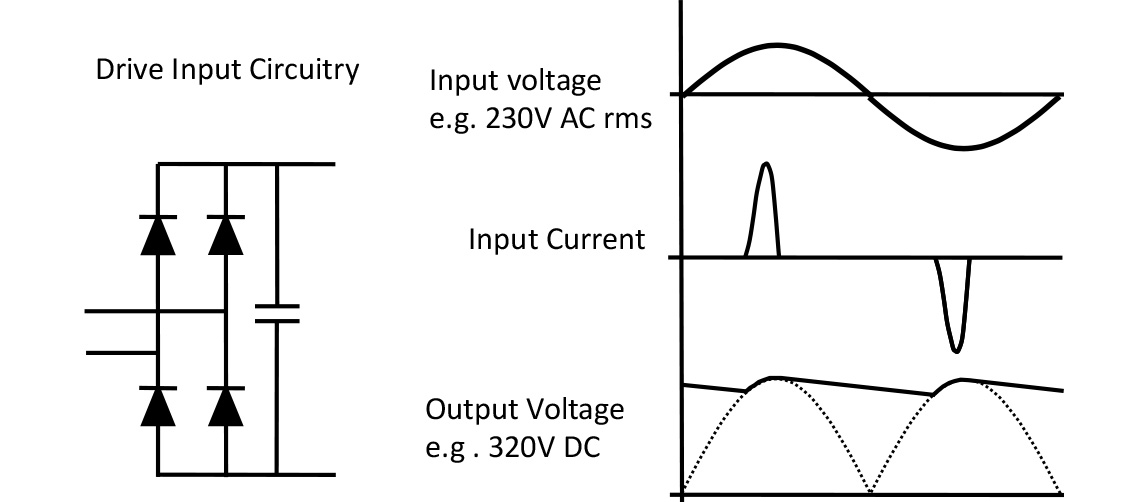
So whether the input is single or three phase the result is the same – a DC voltage of about 320V or so on the DC link capacitor. Of course, if the input voltage is lower or higher than the nominal 230V, the DC voltage will vary as well.
Most drives are designed to operate to full specification over quite a wide voltage range. For example, a 230V Invertek drive will work perfectly well between 200 and 240V with an additional tolerance of +/- 10%. However, it’s recommended that your nominal voltage is between 200 and 240V, with the additional 10% to allow for supply variations. If the voltage falls below about 180V, the drive may not be able to supply enough power to the motor (remember the output voltage will be limited roughly to the input voltage) and if the voltage falls further, the drive’s power supply may switch off. However, the drive will trip on undervoltage before this happens.
If the voltage rises too high, the drive will trip with overvoltage. Very high supply voltages may damage the drive even if it is tripped. This will certainly happen if a 230V drive is connected to a 400V – this happens surprisingly often, so check the voltage of the drive before you connect up.
400V drives are designed for three phase operation. There operating range is generally 380V to 480V, again with a tolerance of +/- 10% to allow for supply variation. It is important that the supply is balanced; that is, the voltage on each phase is within 3% of the other phases. Remember the drive draws current only at the peak of the supply waveform, so a small difference in peak voltage will result in a large difference in phase currents.
Don’t try running a 400V drive on 500V; at the weekend the supply will probably drift up and you’ll have tripped or broken drives on Monday morning.
Supplies are not perfect and often include spikes, dips and surges. Variable frequency drives are protected against voltage surges (and dips), and can absorb a certain amount of energy without damage. But if the energy is too high – for instance, as the result of a nearby lightning strike, the drive will be destroyed. If you expect these ‘spikes’ or surges on your supply, it is advisable to fit additional protection, such as an input choke, which will limit the energy into the drive.
Many (but not all) variable speed drives designed for three phase operation will often run on single phase supplies with derating. Contact the factory before buying your drive to check this out.
Drive manufacturers usually offer additional ranges of drives to cover other voltages. For example, Invertek P2 and Eco variable frequency drives are available with a working voltage of 500 – 600V.
All drives will accept an input of 50 or 60Hz – remember the incoming supply is immediately converted to DC, so actually any frequency reasonably close to 50 or 60Hz is acceptable.
But when would we expect to see odd voltages and frequencies on our supplies? Well, in Europe and many other countries the supply voltage and frequency are well defined. Expect to see 380, 400, 415 volts, pretty well regulated. Other countries are a bit more variable; in the USA you’ll come across 460, 480 or 500V, as well as 208 single or three phase in domestic and light industrial installations. South Africa uses 525V, and Canada has 575V in many places. Back in Europe, 690V is coming into use. Further afield, supplies are not as well regulated, and a nominal 380V could fall to 350V or even lower. So it’s well worth checking exactly what you may expect where you are installing or shipping product; there’s plenty of info on the web.
Grounding or earthing is necessary for all variable frequency drives both for safety and for electromagnetic compatibility. A special case is when drives are operated from an IT supply (See IEC 60364). These supplies are still used in some large plants and have an isolated ground, so they will tolerate ground faults rather than trip. Figure 2 shows an IT supply configuration; check with the factory or operating manual to see how to install your drive on this type of supply.
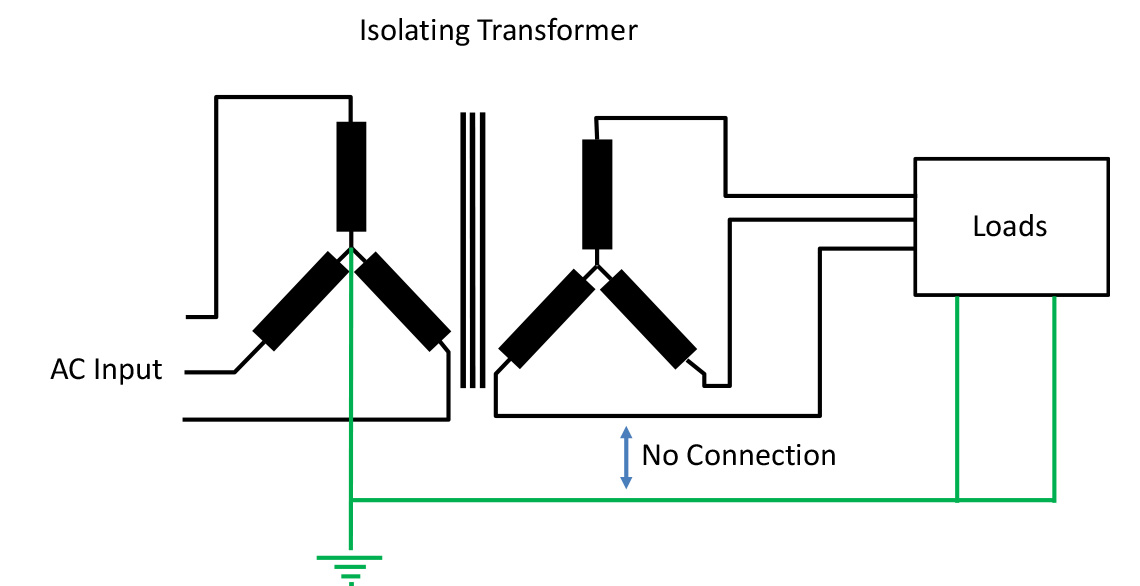
The other application where the voltage is less predictable is when working from a generator supply. Generators can be pretty fickle at the best of times. They are designed to supply linear loads, not rectifiers and capacitors that only take current at the peak of the waveform. So they need some overrating, and care should also be taken when starting up, as the supply voltage and frequency rises slowly – not good for electronics. Invertek have produced an application note which gives detailed information about using a drive with generators (AN-ODP-2-060); find it on the website at www.invertekdrives.com.
Drives can also be operated from DC supplies. There’s not much DC around of course at the sort of voltages we are interested in (i.e. 320V for a 230V drive, and 550V for a 400V drive), but it is possible to connect the DC terminals of several drives together – with care. This is useful when, for example, one drive is motoring (supplying energy to the motor) and another is generating (drawing energy from the motor). If the DC connections of these drives are connected together as shown in Figure 3, the energy from the generating drive will feed the motoring drive, so the net power drawn from the supply is greatly reduced. Always consult the factory before attempting this.
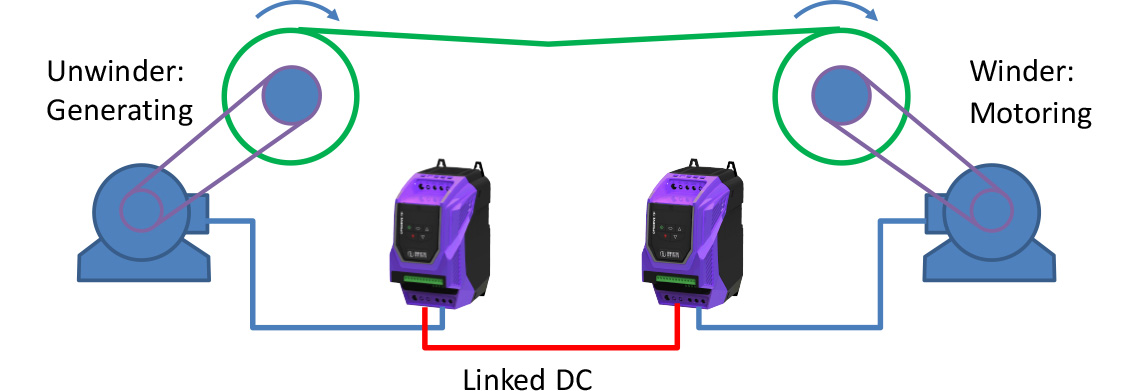